When it comes to choosing a fencing contractor it may be tempting to make a decision based solely on the bid price. Everyone wants a good deal and wants to feel like they are making the right choice for their fence, and their budget.
However, choosing a fencing contractor should involve much more comparison than merely the price. Afterall, a higher price reflects several key factors that result in a quality product that will last. A lower price may seem smart but could very well end up costing you more in the end.
Let’s go over the key factors to consider when reviewing bids from fencing contractors. This will help you understand the price differences you may see, and determine what exactly you are getting in the end.
Know the Quality of Wood the Fencing Contractor Will Use
The last thing a homeowner wants to see on their new fence is warped pieces of wood on what should be a nice, straight, and aesthetically pleasing perimeter. Along the same lines, a wood fence that’s full of knots, cracks, and holes from knots, looks inconsistent and of lower quality. These two issues result from base quality lumber, called “Standard” lumber, and from lumber that has not been properly dried out prior to construction.
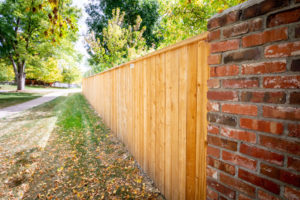
Types of Lumber
“Standard” lumber is the base quality lumber, and you will see many knots, holes from where knots have fallen out, cracks on the ends, and the piece may not be straight. “Standard and Better” is higher quality lumber that’s straighter, has less than 10% of blemishes in it such as knots, and the ends do not have cracks. It’s a mix of quality pieces of wood that meet the “Standard and Better” criteria. The highest quality wood is called “Appearance Grade” and that is typically used for cabinetry and indoor projects, by most contractors. However, sometimes “Appearance Grade” wood is mixed into “Standard and Better” wood.
Integrity Fencing only uses “Appearance Grade” quality lumber for our fences, ensuring a nice-looking and sturdy fence for many years. This type of lumber looks so nice it could be used in the interior of a house.
Drying Wood Out Before Use
The way to avoid warped fence pickets is to allow the wood to naturally acclimate to the climate before construction. In other words: it needs to dry out and lay flat.
Integrity Fencing has our own lumber yard at which we rotate inventory and ensure the wood is dry before using it on a fence project. Unlike when lumber is bought right from a big box store, the wood in our yard has had a chance to dry out and we hand select the pieces that are ready.
Read More: Why You Want Your Fencing Contractor to Use Quality Lumber
Why Good Nails Matter: Don’t Let Your Fence Start Crying
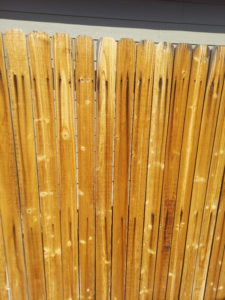
When a fencing contractor wants to cut their costs, they may use a cheaper nail such as an electromagnetic nail. This lower cost nail results in lower quality: it will eventually corrode and rust when exposed to moisture over time. You may see the rust streaks a year or two after your fence installation, depending on the moisture where you live, how often your sprinkler hits the fence, etc.
The simple prevention for a rust-streaked fence is to go with a quality nail from the beginning. Make sure your fencing contractor uses hot-dipped, galvanized nails that will not rust out.
Read More: Rust Teardrops, What Your Fence is Crying About
Fence in a Day? Know Your Fencing Contractor’s Way
Find out how quickly your fencing contractor will turn the job around. Do they require multiple crews coming out across multiple days? Some fence companies will take three to four days to finish a fencing job. This is because they have one crew to set the posts, then have to schedule a second crew to finish the job. This can be an issue for homeowners with dogs, children, or anything on the other side of the fence that they don’t want in their yard.
Or is the fencing contractor a ‘turnkey company’ that can do both the set and finish in one day? A quality contractor that uses one crew can typically finish a tear down and rebuild, for up to 250 feet of fence, in one day. Integrity Fencing accomplishes this by having just one crew for the entire job, and using Quik-Rok a concrete additive that hardens in 40 minutes (as long as the air temperature is above 30 degrees).
While a turnkey company will cost more to hire, the speed and convenience of having a new fence in one day is tough to beat.
Done Dirt Cheap: Where Does Displaced Dirt from Fence Post Holes End Up?
One aspect of a fencing project that most people don’t think about is: where does all the displaced dirt fence post holes go after the job is done? If you are going with the cheapest bid, you can bet that the fencing contractor is going to just throw the dirt anywhere in the yard and leave it. Why is this a problem? If a homeowner has landscaping in their yard, a lawn, or any kind of landscaping fabric, the dirt thrown over it will eventually grow weeds. The dirt will have seeds and roots of weeds and when it settles in between landscaping on top of fabric, or among grass, weeds will eventually sprout.
Make sure the contractor you choose factors in the cost to remove the dirt they dig out and take it with them.
Recognizing a Poor Fencing Job
In the realm of, “you get what you pay for”, it’s quite easy to spot a shotty fencing job that was done by a cheap contractor. A poor fencing job will have big gaps between pickets, unevenness across the top of the fence, obvious poor craftsmanship, low quality wood, rusty bleeding nails, and mixed and matched pickets (resembles a quilt).
The homeowner may have saved money at first, but sometimes a poor quality fence is so badly done that it can’t even be fixed and must be rebuilt entirely. In the end, the cost is much higher than if the fence had been done well in the first place.
Your Fencing Contractor Should Leave You Worry Free
What does a homeowner want when their fencing contractor completes the job and leaves? They never want to think about their fence again other than that it’s doing its job, and looks nice at the same time.
When you understand why there is a price difference between fence project bids, it makes the decision much easier. The little things matter on a construction job; things that will have an impact on customer satisfaction down the line.